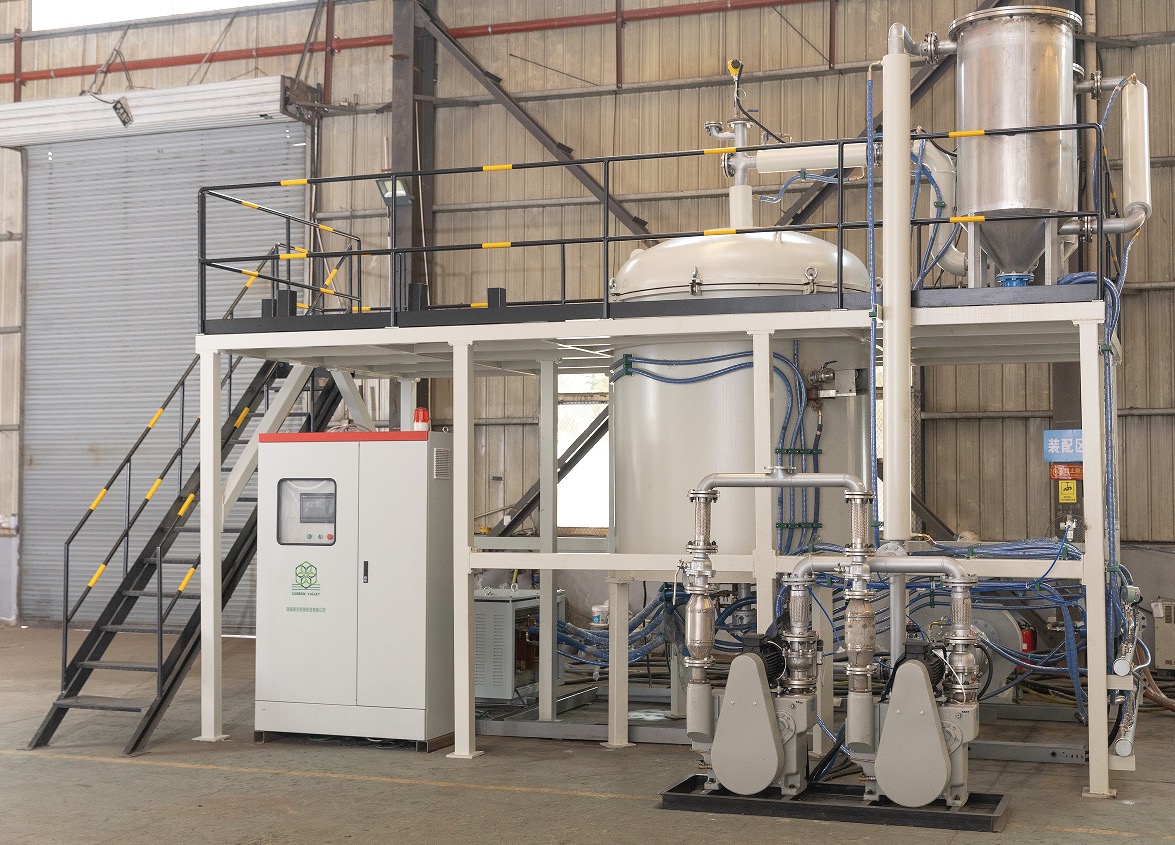
從設(shè)備運行原理來看,氣相沉積爐的能耗主要來源于加熱系統(tǒng)、真空系統(tǒng)和氣體控制系統(tǒng)。以化學(xué)氣相沉積(CVD)爐為例,加熱系統(tǒng)需將反應(yīng)腔室升溫至幾百甚至上千攝氏度,以促使氣態(tài)反應(yīng)物在高溫下發(fā)生化學(xué)反應(yīng)并沉積在基底表面。在高溫長時間運行過程中,加熱元件持續(xù)消耗大量電能,約占總能耗的40%-60%。真空系統(tǒng)則通過真空泵不斷抽氣,維持反應(yīng)腔室的真空環(huán)境,避免空氣干擾沉積過程,其能耗占比約為20%-30%。氣體控制系統(tǒng)用于精確控制反應(yīng)氣體和載氣的流量與壓力,這部分能耗占比約10%-20%。
不同類型的氣相沉積爐能耗差異顯著。物理氣相沉積(PVD)爐主要依靠物理過程,如蒸發(fā)、濺射實現(xiàn)材料沉積,相比CVD爐,無需高溫化學(xué)反應(yīng),加熱需求相對較低,因此整體能耗也較低。磁控濺射PVD爐在制備金屬薄膜時,每生產(chǎn)一平方米薄膜,能耗約在5-10千瓦時;而CVD爐在制備相同面積的半導(dǎo)體薄膜時,能耗可能達到15-25千瓦時。原子層沉積(ALD)爐雖然能實現(xiàn)原子級別的精確沉積,但由于沉積過程緩慢,需要多次循環(huán),單位時間內(nèi)處理量小,在同等生產(chǎn)規(guī)模下,能耗甚至可能高于CVD爐。
工藝參數(shù)設(shè)置對氣相沉積爐能耗影響巨大。反應(yīng)溫度、壓力、氣體流量等參數(shù)的細微調(diào)整,都可能改變能耗。提高反應(yīng)溫度雖然能加快沉積速率,但會顯著增加加熱系統(tǒng)的能耗;降低反應(yīng)壓力有助于提高沉積質(zhì)量,但會使真空系統(tǒng)負荷增大,能耗上升。若將CVD爐的反應(yīng)溫度從800℃提升至1000℃,能耗可能增加30%-50%。因此,合理優(yōu)化工藝參數(shù),在保證產(chǎn)品質(zhì)量的前提下,尋找能耗與生產(chǎn)效率的平衡點,是降低能耗的關(guān)鍵。
設(shè)備的先進程度也與能耗息息相關(guān)。新型氣相沉積爐采用高效加熱元件、智能溫控系統(tǒng)和節(jié)能真空泵,相比傳統(tǒng)設(shè)備,能耗大幅降低。配備陶瓷纖維保溫層的加熱腔室,能有效減少熱量散失,使加熱系統(tǒng)能耗降低15%-20%;變頻控制的真空泵可根據(jù)實際需求自動調(diào)節(jié)抽氣速率,降低真空系統(tǒng)能耗10%-15%。此外,自動化程度高的氣相沉積爐,通過精準控制工藝過程,減少因參數(shù)波動導(dǎo)致的重復(fù)生產(chǎn),間接降低能耗。
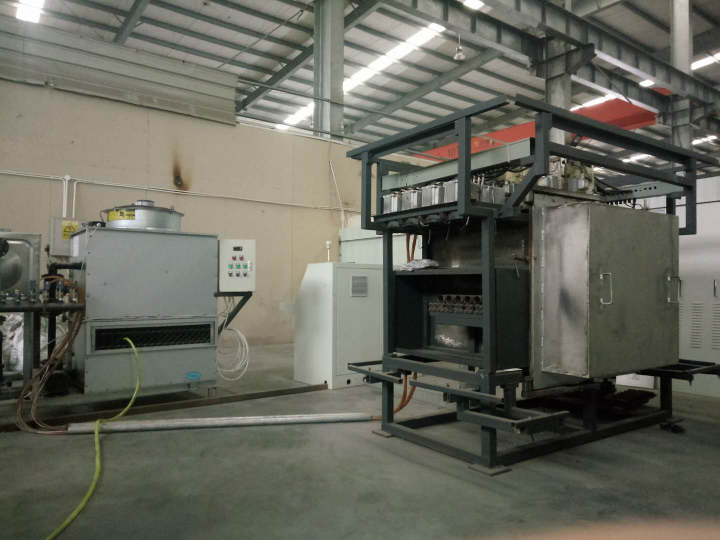
綜上所述,氣相沉積爐能耗受設(shè)備類型、工藝參數(shù)和設(shè)備先進程度等多種因素影響。在實際生產(chǎn)中,企業(yè)可通過選擇合適的設(shè)備、優(yōu)化工藝參數(shù)和采用先進技術(shù),降低氣相沉積爐的能耗,在保障生產(chǎn)質(zhì)量和效率的同時,實現(xiàn)節(jié)能減排,提升企業(yè)的經(jīng)濟效益和環(huán)境效益。感謝閱讀,想了解更多歡迎繼續(xù)閱讀《氣相沉積爐多少錢,2025氣相沉積爐價格》。